RHT-SS Frameset
Single speed MTBs have seen a decline in popular acceptance but they do still have a passionate following among riders in the sport. We have always had a soft spot for this kind of cycling minimalism so when we were asked to design a frame from the ground-up to be our take on the ultimate single speed, how could we resist?
As would be fitting for a minimalist bike the list of requirements was short: make it a dedicated singlespeed, use sturdy dropouts, clear a 2.4" tire, and fit the rider properly. As is often the case with minimalist products, meeting all of these requirements and looking clean took quite a bit of effort but the finished product made it all worth the effort.
Frame Design
To start off, we interviewed our customer to better understand how the bike should fit and understand how they expected it to handle. In this case, what they were looking for was a bike that was more stable than the XC race bikes they were used to but with a more traditional MTB fit geometry than most off-the-shelf, modern "forward geometry" framesets. From those starting points, we landed on a 68 deg headtube angle, 435mm chainstays, and a 65mm BB drop as a compromise of all of these features.
With the geometry nailed down, we needed to check the nuts and bolts of the design through the use of Finite Element Analysis (FEA). Using this program, we are able to check that the frame will last for the riders lifetime and match our stiffness requirements for the application.
We were able to determine that we would need to have a very strong chainstay yoke to provide the tire and chainring clearance required while achieving the stiffness values we were targeting. We also discovered that we couldn't use dropouts designed for traditional double-diamond frames due to the stress created. Our two main focal points for our engineering efforts then lay in redesigning the chainstay yoke and designing specific dropouts for our aggressive dropped seatstay design.
The chainstay yoke design started from a collection of drawings that helped us outline our ideas and develop a design that would be readily manufactured with the tools at our disposal. Utilizing a series of 3D prints, we started to sort out the ideas that didn't work and finally hit upon two different designs for a laser cut and hand-formed sheet metal creation that we could use. These two designs were later refined to a single model after we spent time building metal prototypes before including the finished version in the final frame.
Dropouts for this build were the most critical point of our engineering exercise due to the stresses that would occur with conventional dropouts. Additionally, our customer requested something a more unique aesthetic which matched our desire of combining our passions for clean industrial design and engineering functionality. Once again, we started from a sketch and iterated the design to be optimized for our method of manufacture which, for the dropouts, was CNC machining. Working with a local machinist to optimize the parts, we produced a beautiful finished product we can incorporate into the frame.
The end result of this dropout work is a lightweight machined component that is compatible with Paragon Machine Works dropout sliders for easily sourced options on your dropouts. Should our customer ever decide that the singlespeed life is not for them, they can easily change out to a dropout with a derailleur hanger and start shifting gears once more.
Fabrication
Every one of our frames is built in steel with the use of fillet brazing to create the structure but we also use our machine shop to fabricate all of the smaller components required to help piece all of the tubes together.
An example of this type of machined and brazed sub-assembly are our headtube reinforcement rings. We've written an in-depth post on our process for creating these parts that can be found here if you are interested in more details. For this application, we modified the design to reduce the overall height of the reinforcing rings and to make them easier to machine. The final product, including the slots cut in for venting, is shown below.
We also used a machined collar on top of a thin-wall 4130 35mm tube as our seat tube. This allowed us to increase the wall thickness at the point where the tubes were brazed together to help maintain concentricity and increase the strength in this highly loaded area.
The last tricky piece of the fabrication was the dropped seatstays where they blend into the monostay at the downtube. This was a combination of a number of different elements with a gusset brazed onto the downtube, a tapered ovalized tube to create the monostay and of course ensuring that the seat stays bends matched from side-to-side and had enough clearance to all the components at the rear of the bike. Unfortunately, we didn't take any photos while we built up the seatstays, but the raw nature of the frame helps to reveal all the manufacturing details.
From here, the frame will be powdercoated for it's final finish. It's a simple but durable finish that will cause no issues for the customer and is in keeping with the minimalist nature of a single speed frame. As you can tell from the previous photos, we haven't powdercoated the frame just yet as we wanted to show the final work before it was hidden under the protective powdercoat finish.
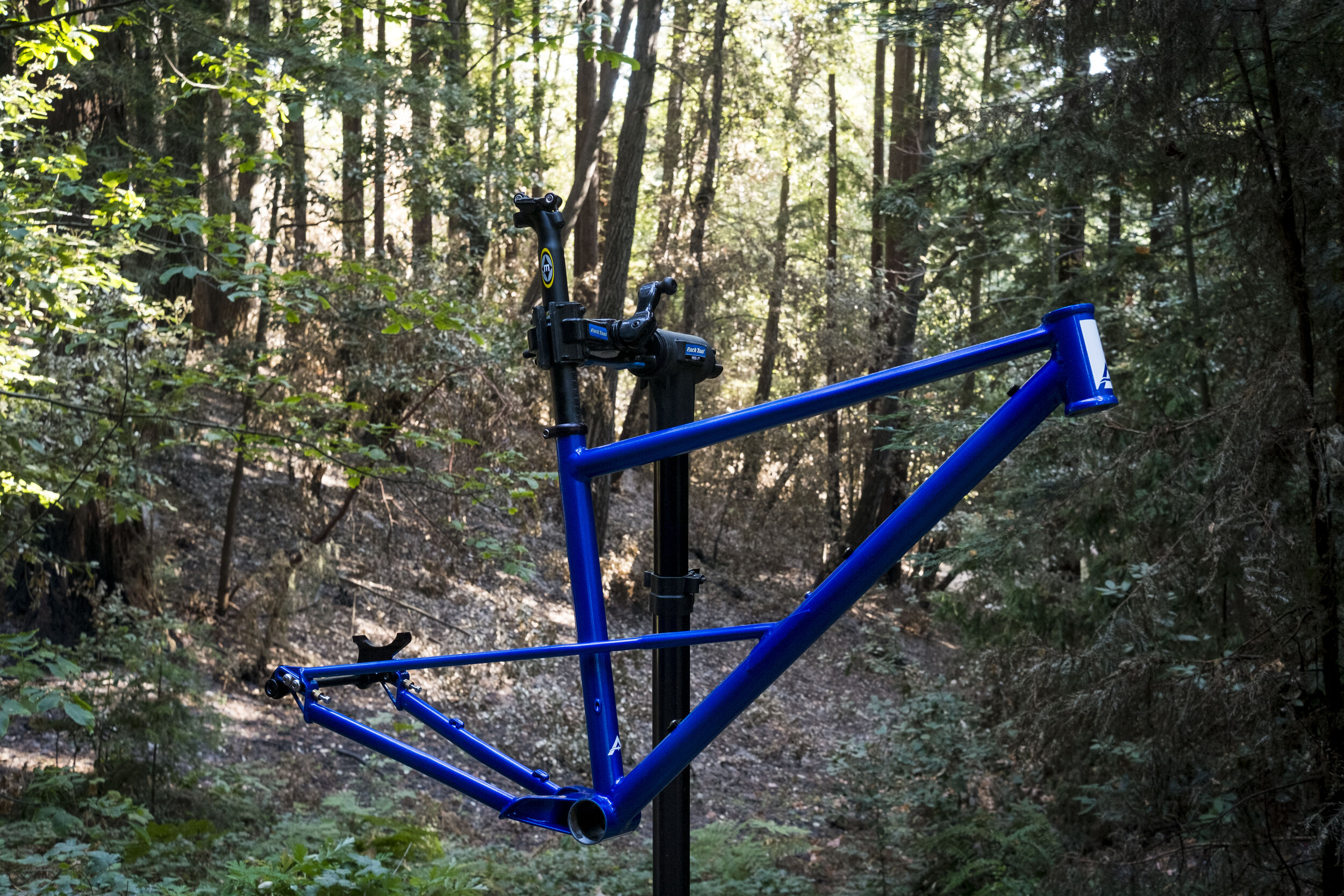
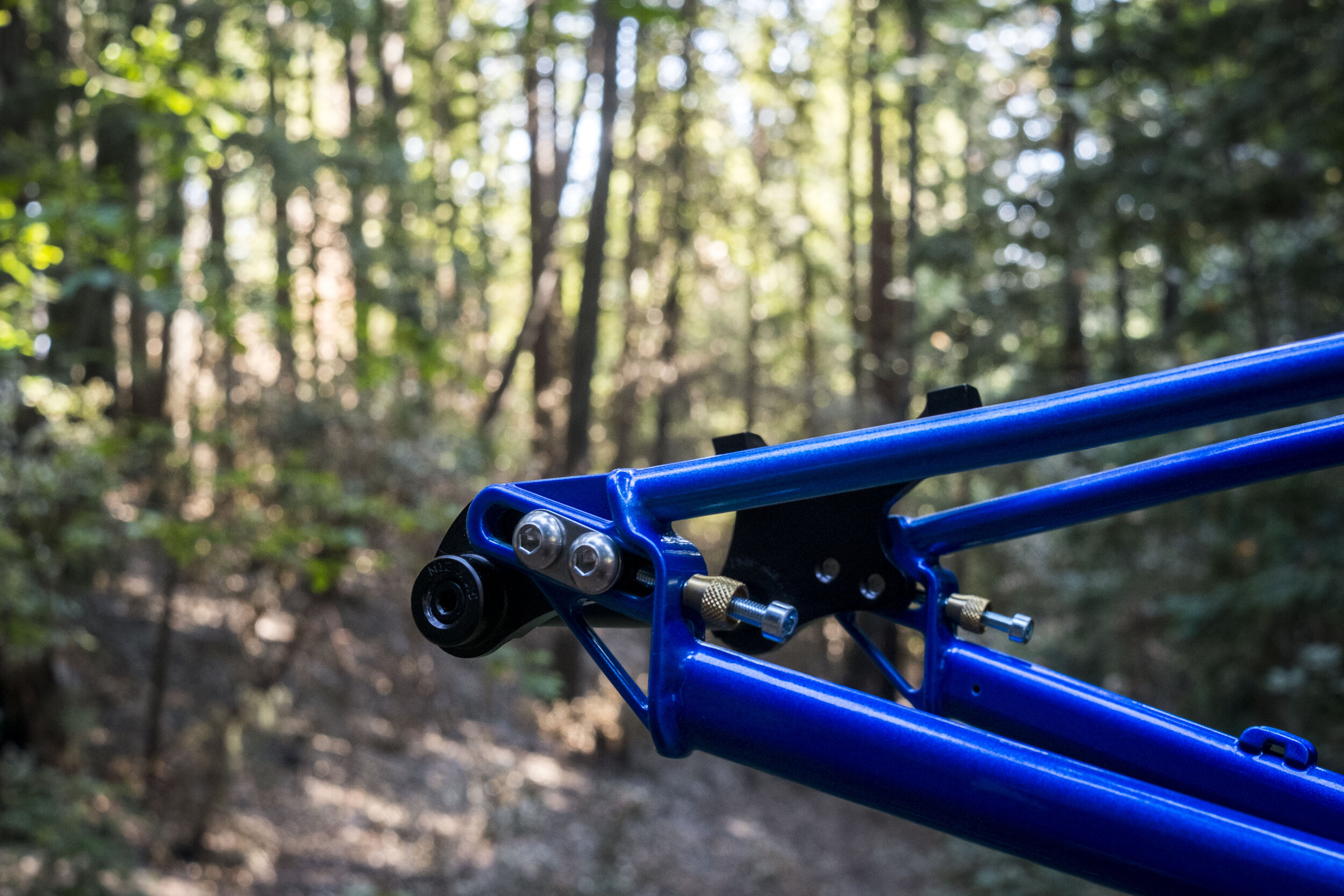
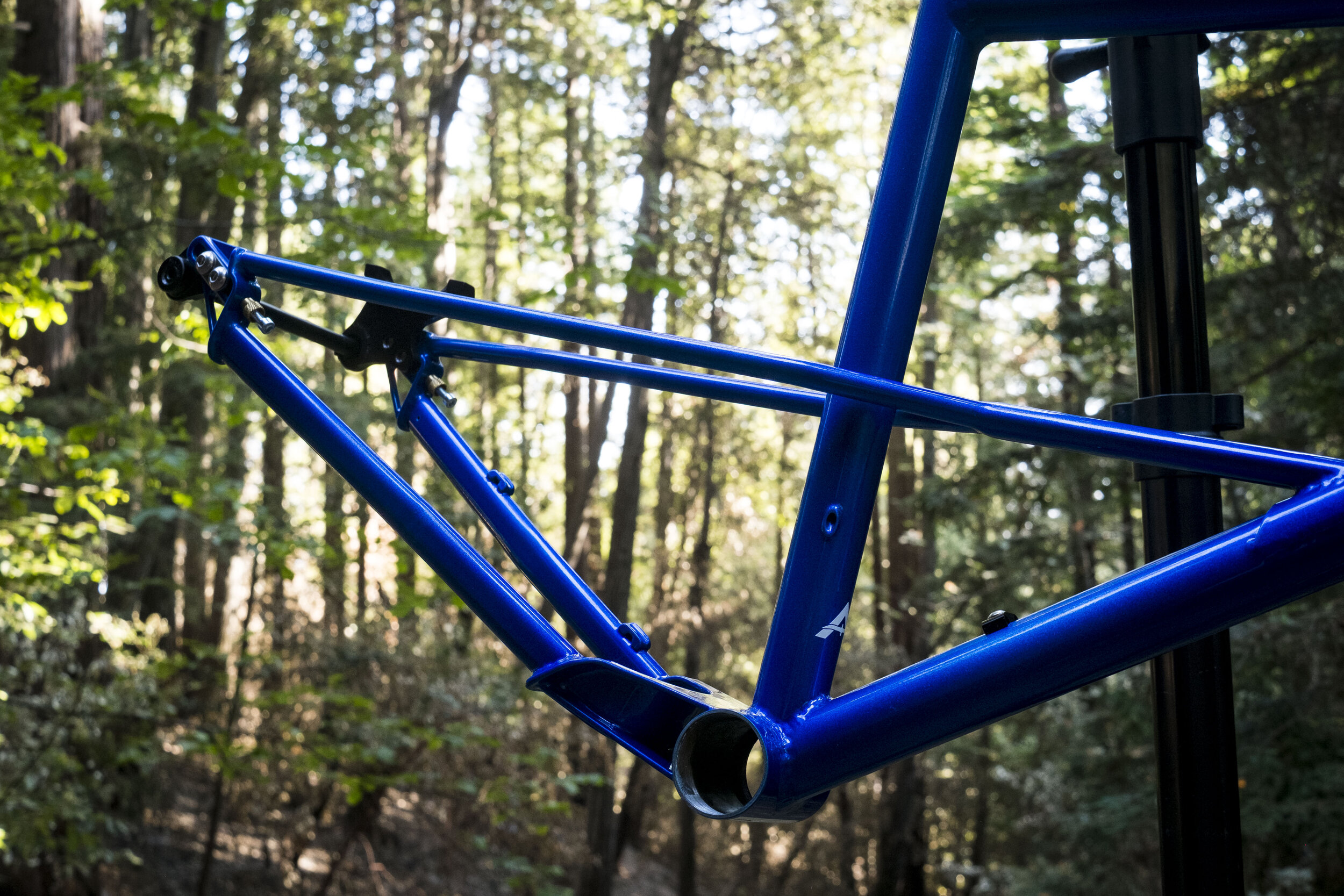
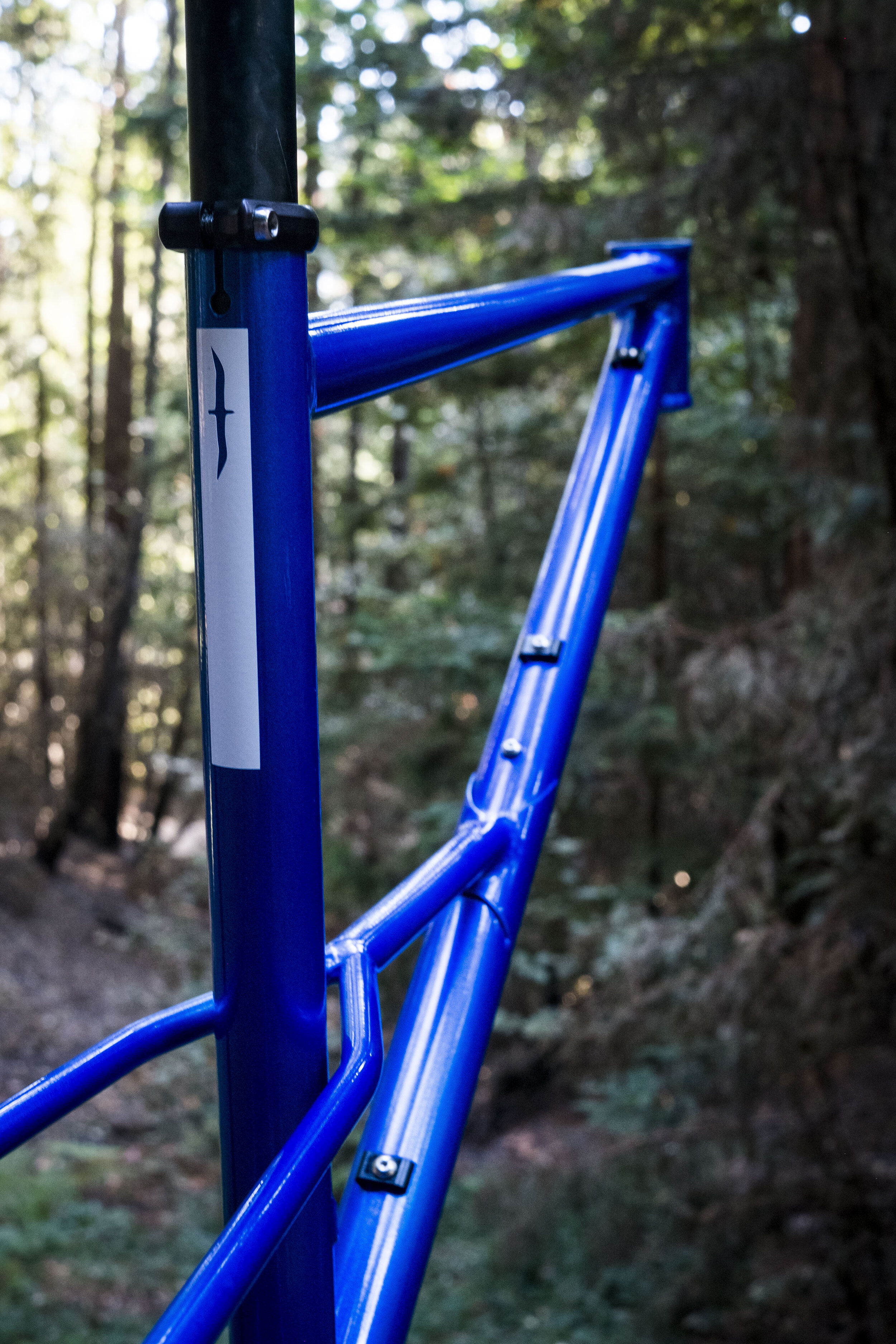
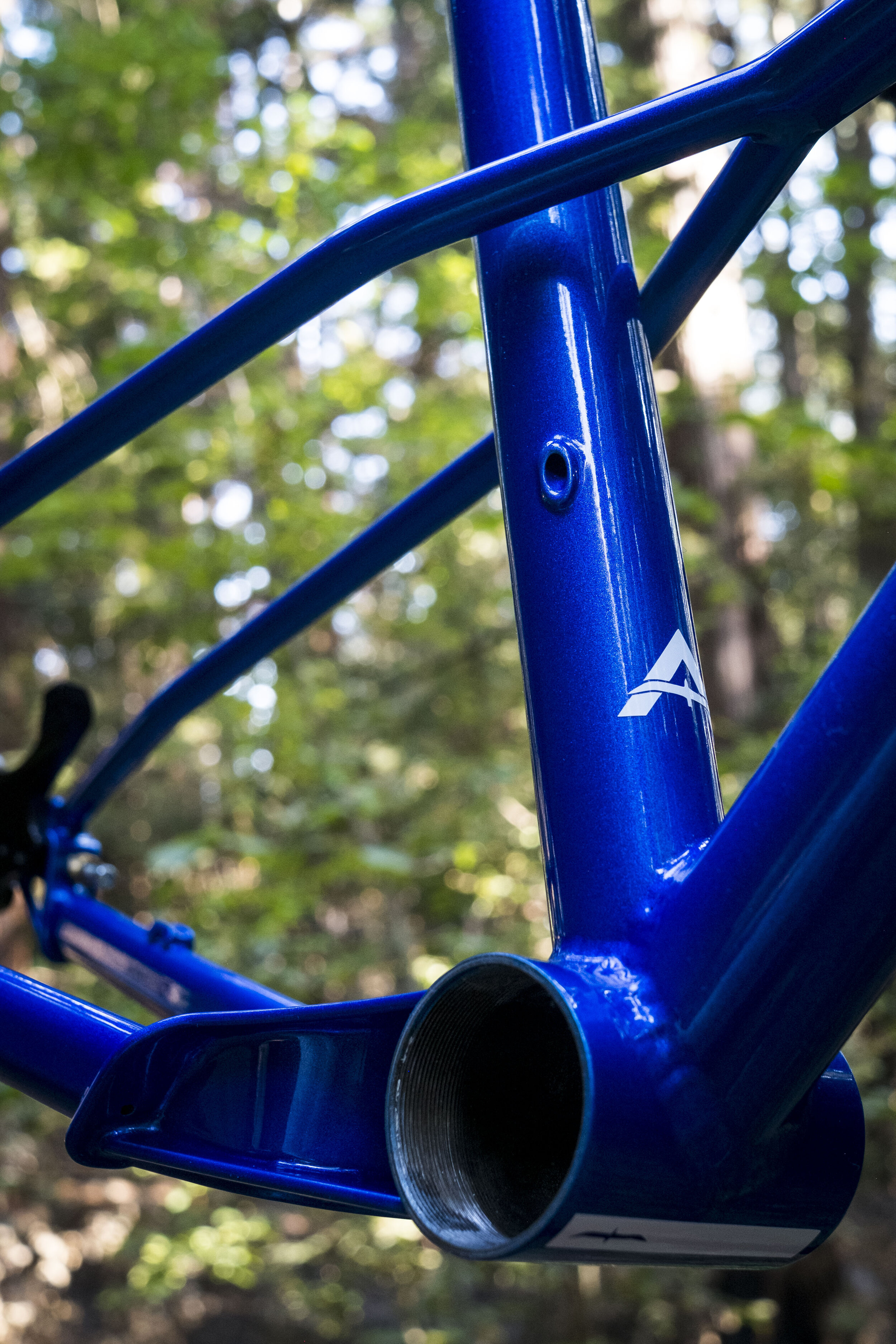
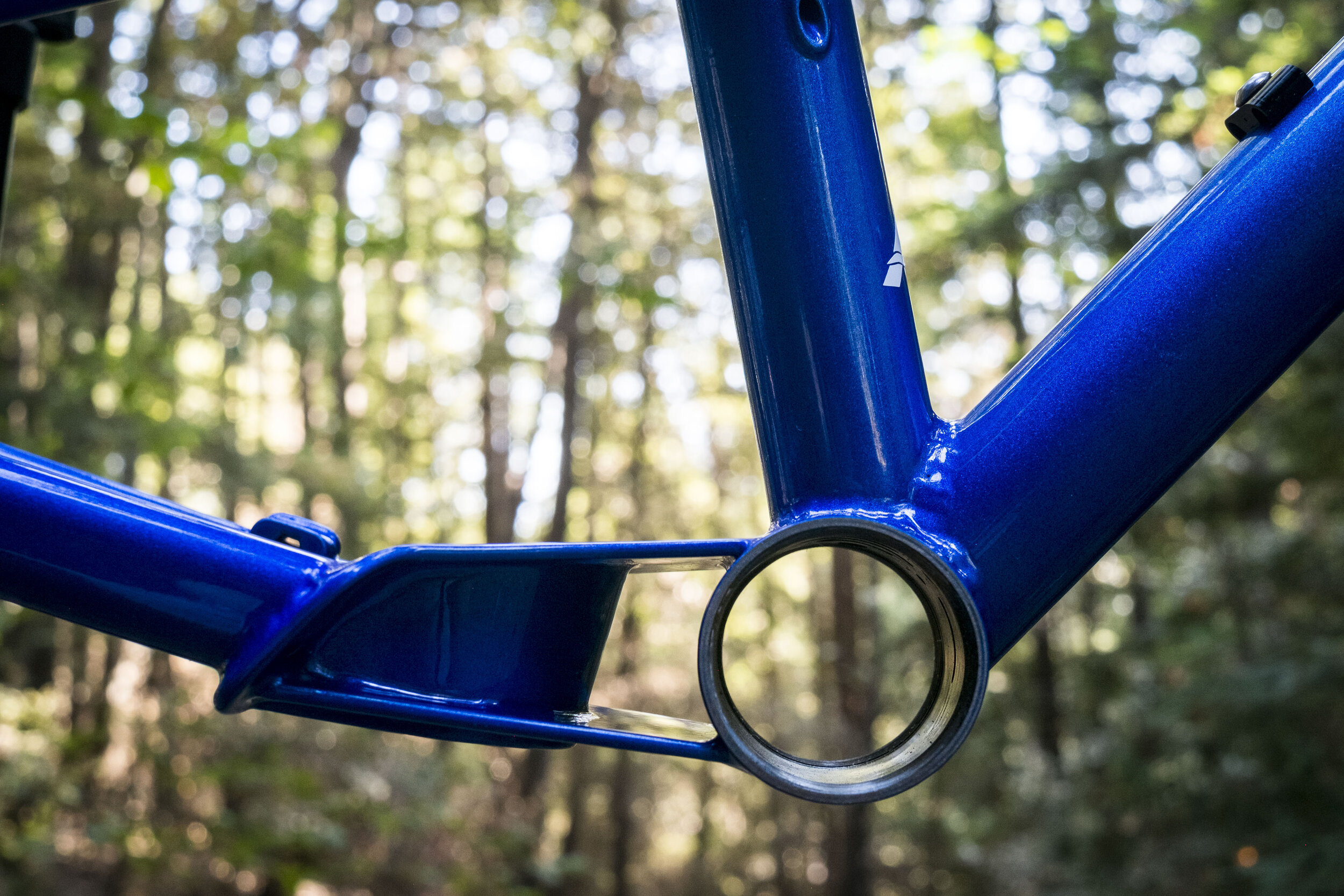
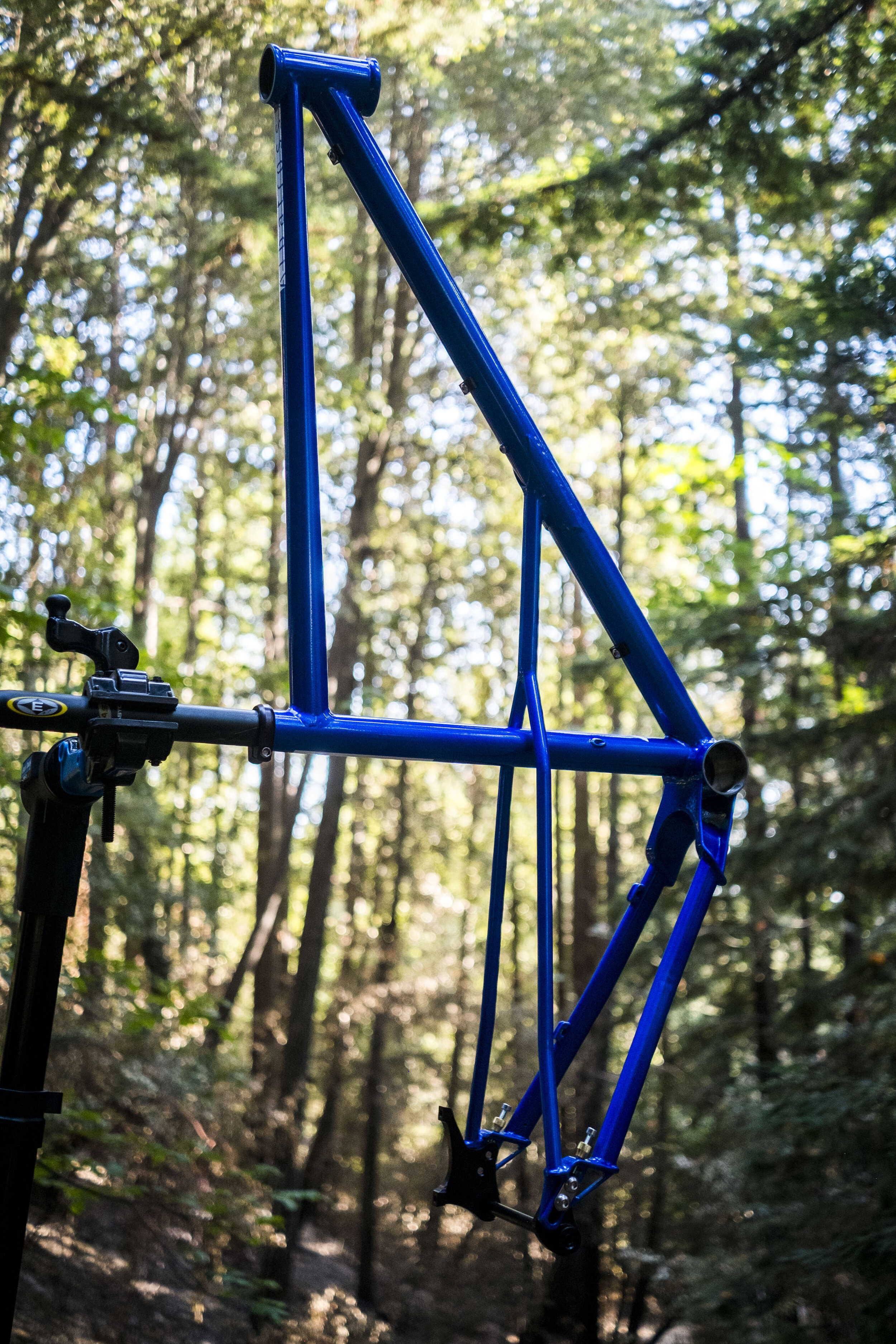
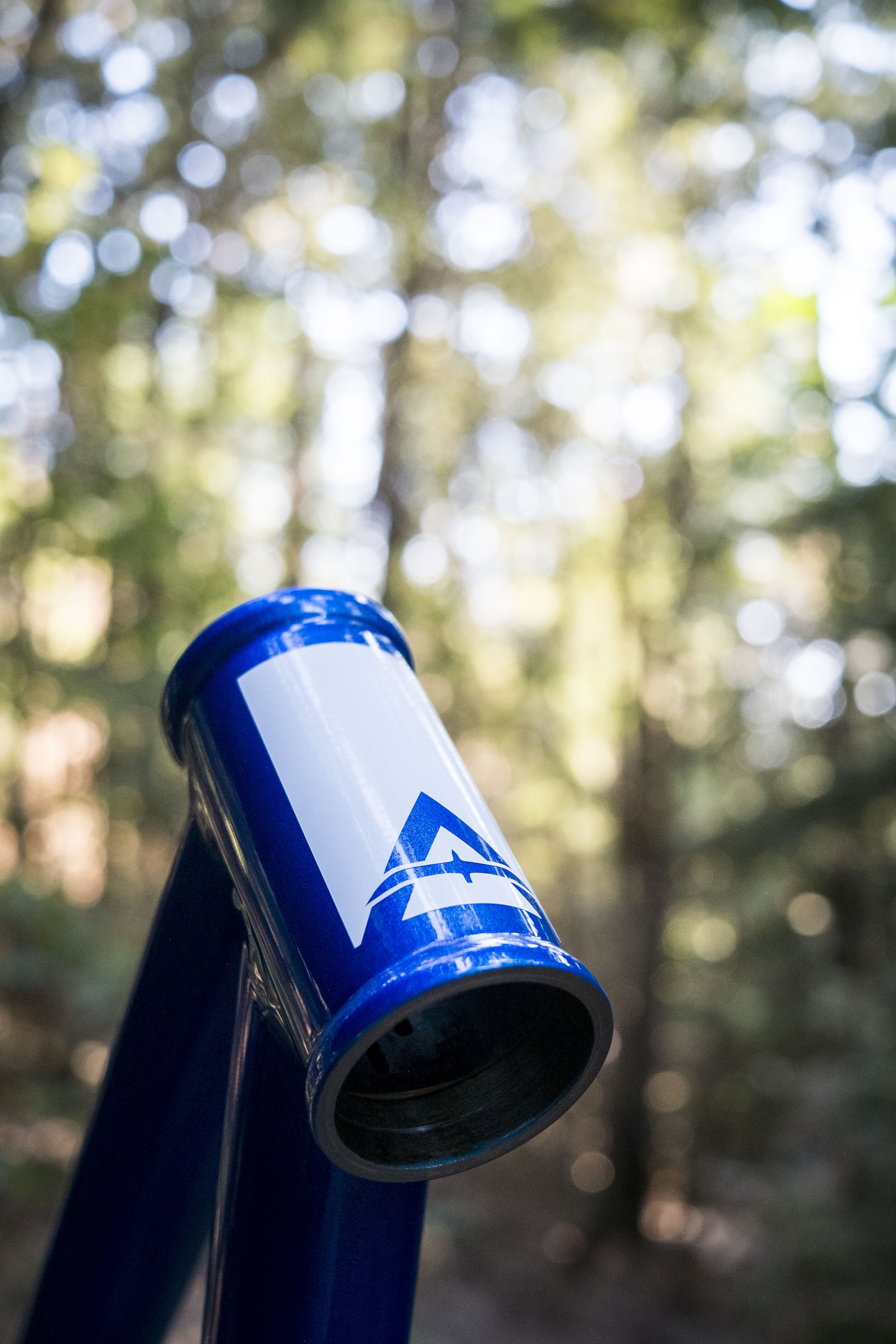
Building this singlespeed frame took quite a bit of experimentation to get it right and we are happy that the finished result fulfills every one of the customers requirements. With the difficult engineering work to make this singlespeed frame complete, we look forward to building more of these frames in the future.
Until next time: Ride Fast, Ride Far.